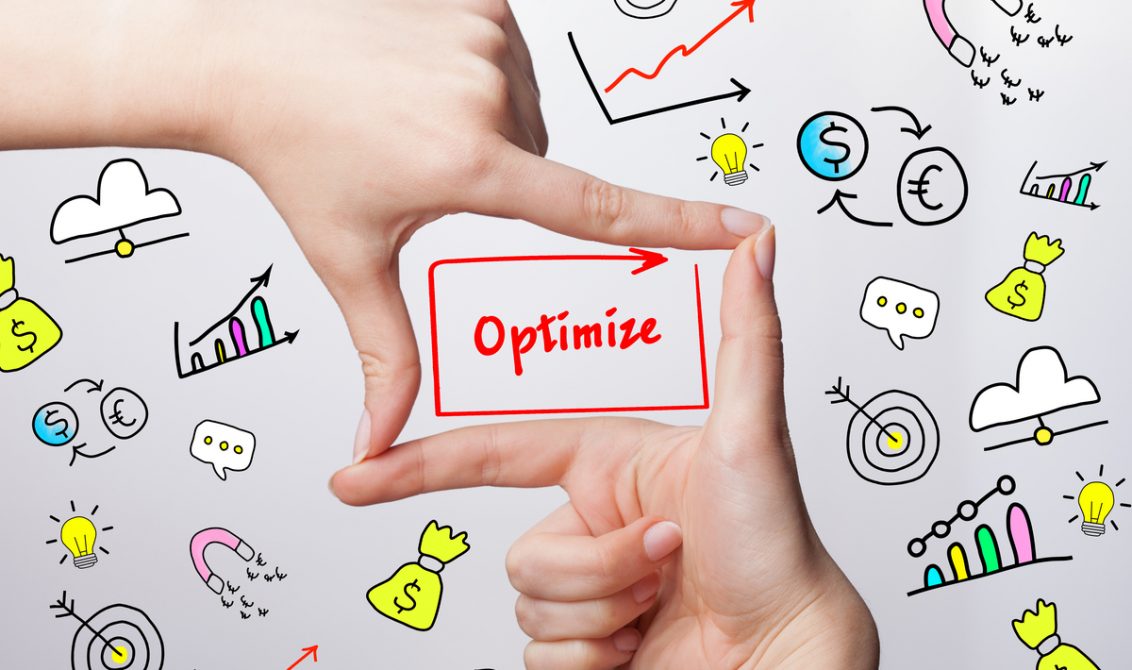
L’intervista a Carlo Poloni, Presidente di Esteco S.p.A.
Nelle grandi industrie c’è fermento. La necessità di velocizzare la produzione e mettere a punto prodotti ogni giorno più complessi sotto il profilo progettuale, spinge al reperimento di soluzioni sempre più innovative, precise e che diano risultati concreti e ripetibili nel tempo. Lo ha capito bene Esteco, azienda specializzata nella ricerca e nello sviluppo di soluzioni software per l’automazione, l’integrazione e l’ottimizzazione di tutte le fasi dello sviluppo ingegneristico.
In cosa consiste il lavoro di Esteco?
Sviluppiamo software avanzati con l’obiettivo di semplificare il lavoro degli ingegneri, mettendoli in condizione di gestire in modo efficace progetti multidisciplinari complessi. In particolare forniamo una soluzione tecnologica che consente di integrare in un’unica piattaforma molteplici software di simulazione e analisi utilizzati nella fase di progettazione. Una volta impostato questo workflow la piattaforma consente di automatizzare il calcolo applicando algoritmi di ottimizzazione. Infine, la mole di dati prodotta può essere facilmente esplorata attraverso strumenti di visualizzazione, analisi dei dati e supporto alle decisioni.
Come funzionano gli algoritmi di ottimizzazione?
Una volta impostati gli input e definiti gli obiettivi del lavoro di progettazione, il nostro software cerca la soluzione di “compromesso” ottimale per realizzare quel determinato prodotto. Si definisce soluzione “di compromesso” perché deve tenere conto di numerosi parametri come il costo e le prestazioni. Ad esempio, semplificando di molto il problema, quando viene progettata l’ala di un aereo vogliamo che sia più leggera possibile, ma deve anche poter resistere al carico e garantire la massima efficienza aerodinamica.
Il nostro software si interfaccia con il programma che simula il comportamento fluidodinamico dell’aereo e modifica in automatico i parametri geometrici in modo da creare diverse configurazioni di cui viene valutata la resistenza. Gli algoritmi consentono di individuare la configurazione di parametri migliori: il miglior compromesso tra resistenza e leggerezza.
Come nascono i vostri software?
Sono prodotti internamente dal nostro staff di tecnici altamente qualificati. Il team è composto da professionisti di varia natura (abbiamo matematici, fisici, programmatori, ecc.), ognuno dei quali si occupa di un aspetto specifico del software. C’è, ad esempio, chi ne cura la grafica e l’usabilità, chi implementa integrazioni con altri software, chi affina gli algoritmi, ecc.
Quali sono gli ambiti di applicazione e quali i vantaggi apportati?
Il nostro target sono le aziende mediograndi e il 50% dei nostri clienti appartiene al settore automotive. Le applicazioni dei software però sono numerose, pensiamo solo all’aeronautica, agli impianti industriali ma anche agli elettrodomestici: parliamo sempre di prodotti complessi che richiedono di tenere simultaneamente in considerazione molteplici requisiti (sicurezza, risparmio energetico resistenza strutturale, confort, ecc.). Tutti questi settori traggono quindi numerosi vantaggi dall’utilizzo dei nostri software: la razionalizzazione del processo di design, ad esempio, o la riduzione dei tempi di calcolo (che viene svolto in modo automatico risparmiando numerose ore di lavoro umano), la maggiore efficienza e la ripetibilità dei processi e delle analisi. Inoltre, ricorrendo ai nostri software la possibilità di errore umano viene totalmente eliminata.
In generale, quali sono i modelli matematici che tornano utili alla progettazione industriale?
Anche in questo caso si possono fare tanti esempi. Usiamo tutti i modelli necessari all’ottimizzazione di tipo combinatorio (dal calcolo differenziale a quello delle probabilità, fino alla teoria dei giochi). Abbiamo persino i n t ro d o t t o l’algoritmo di Nash come supporto alle decisioni. Ricorriamo, poi, a processi gaussiani. Insomma, c’è di tutto.
Ci racconta qualche esempio di aziende che hanno utilizzato i vostri software, nei settori dell’automotive, dell’industrial equipment o turbomachinery?
Partiamo dai treni, in particolare i treni Zefiro 380 prodotti da Bombardier. Hanno vinto la gara per la fornitura di Frecciarossa a Trenitalia grazie alla loro forma aerodinamica realizzata con il nostro software. L’obiettivo di Bombardier era quello di trovare un modello Pareto-ottimale che allo stesso tempo desse bassa resistenza e avesse buone caratteristiche di stabilità. La soluzione è stata ottenuta con il nostro software che ha permesso non solo di integrare i diversi strumenti CAE (Computer-Aided Engineering) in uso presso Bombardier, ma anche di guidare il processo di modifica e simulazione fornendo gli strumenti di analisi necessari per l’interpretazione statistica dei risultati. Il nostro software utilizza algoritmi genetici per determinare le soluzioni Pareto-ottimali, combinando i modelli 3D e le simulazioni di resistenza aerodinamica e di stabilità di vento trasversale. I tecnici di Bombardier hanno considerato ben sessanta differenti parametri in fase di modellazione, compresi elementi come le coperture esterne, la cabina e i vincoli di carattere ergonomico. L’azienda è stata in grado di ridurre la resistenza aerodinamica del treno del 20%, ottenendo una riduzione del consumo energetico di circa il 10%. Gli ingegneri Bombardier sono stati in grado di scegliere tra una selezione di configurazioni, al fine di trovare la soluzione ottimale che fornisse un compromesso tra preferenze stilistiche, rendimento energetico, massima stabilità e sicurezza.
Un’altra case history interessante è quella di BMW. Il centro di R&D che lavora ai motori diesel ha usato mode FRONTIER per ottimizzare il sistema di raffreddamento del motore diesel a sei cilindri e per supportare le fasi di validazione del modello termico recentemente aggiornato. Grazie alle sue capacità avanzate di integrazione, automazione e ottimizzazione, il software ha consentito di definire un quadro preciso per il confronto e l’ottimizzazione di differenti pacchetti di raffreddamento che consentissero di aumentare l’efficienza del motore e ridurre il consumo di carburante. Per identificare le configurazioni migliori, il team di ingegneri di BMW ha utilizzato Kuli, uno dei più popolari software di simulazione di gestione termica disponibili, supportato da simulazioni 3D CFD (Computational Fluid Dynamics).
L’utilizzo dei due software ha permesso agli ingegneri di rilevare la configurazione ottimale per i principali parametri fondamentali, cosa che ha portato a una più rapida identificazione dei migliori coefficienti di scambio termico e inerzia termica del motore. Trasferendo il modello sul veicolo reale, alcuni parametri hanno indicato oscillazioni durante i cicli di validazione, in particolare la temperatura dell’olio che ha mostrato un’oscillazione più grande in fase di salita. Grazie all’ottimizzazione eseguita sul ciclo in fase di salita i parametri del motore sono stati affinati, con un conseguente e significativo miglioramento nella misurazione sulla pista di prova.
La squadra BMW ha potuto creare un modello di sistema di raffreddamento affidabile, compatibile con le nuove linee guida di prova e abbastanza preciso per essere riutilizzato per il confronto e l’ottimizzazione dei pacchetti di raffreddamento differenti. Inoltre, le funzionalità di automazione di mode FRONTIER, insieme con i suoi potenti algoritmi di ottimizzazione, hanno consentito la messa a punto automatica dei parametri che hanno sostenuto e ridotto il numero di passi di validazione del modello.
Altro esempio è quello di Alenia Aermacchi, azienda capofila del design team Green Regional Aircraft (GRA), impegnata a progettare aerei di linea regionali a impatto ambientale ridotto. Il loro obiettivo era ridurre l’impatto ambientale dei vettori regionali riducendone il peso, migliorando l’efficienza aerodinamica, raggiungendo migliori performance operative e al contempo rispettando gli standard per il controllo di emissioni e rumore. Perseguire simultaneamente obiettivi diversi, come la riduzione del coefficiente di resistenza o dell’impatto ambientale nelle fasi di decollo e atterraggio, consente di migliorare la performance ambientale complessiva misurata da indicatori come il consumo di carburante e la produzione di rumore.
Durante la ricerca delle soluzioni più promettenti per questi aerei di nuova generazione, i designer hanno analizzato e ottimizzato due diversi profili alari. La prima configurazione, detta “thin”, è servita per migliorare la performance aerodinamica, senza imporre vincoli allo spessore dell’ala.
La seconda configurazione “thick” è stata definita con l’obiettivo di ridurre il peso dell’ala.
Il nostro software ha permesso di considerare obiettivi complessi in un contesto simultaneo e ottenere miglioramenti significativi per entrambe le configurazioni. L’automazione di processo guidata dal potente workflow del software ha permesso di esaminare 20.000 design per il profilo alare 2D, integrando l’analisi aerodinamica e strutturale simulata grazie e codici in-house. Una volta identificato il candidato ottimale per i profili, l’analisi CFD è stata validata su un modello di geometria parametrica 3D realizzato in CATIA: i buoni risultati dimostrati dagli indicatori 2D di performance aerodinamica sono stati confermati.
I vantaggi apportati dal nostro software sono stati molteplici: innanzitutto, un miglioramento di performance aerodinamica del 2.5% e una diminuzione del peso del 4%; poi, il processo a due fasi di ottimizzazione dell’ala ha guadagnato un notevole livello di efficienza; gli strumenti di analisi statistica hanno consentito una visione delle relazioni tra i parametri di aerodinamica utili a impostare la strategia di ottimizzazione; infine, lo strumento di supporto decisionale MCDM (Multiple Criteria Decision Making) ha fornito uno schema utile alla classificazione del set di soluzioni ottimali e ha guidato il team nella scelta del miglior candidato.