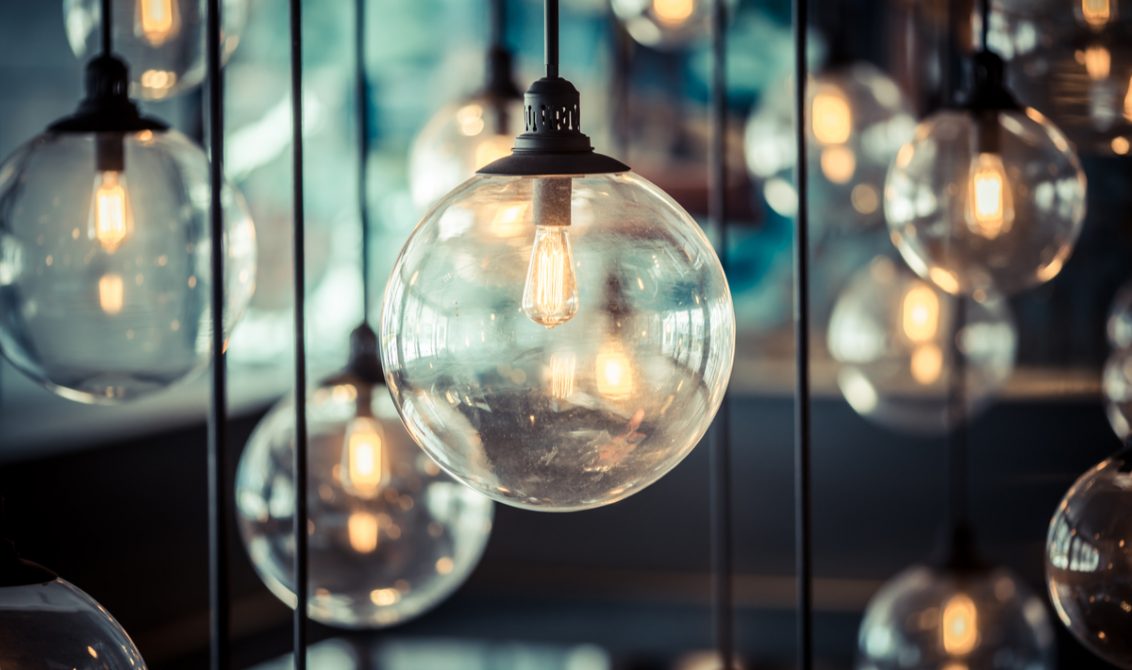
Come si verifica la sicurezza di un apparecchio di illuminazione? Come ci si accerta se è stato progettato e costruito in conformità alle norme?
Vediamo passo passo le principali verifiche e prove che deve subire un apparecchio di illuminazione che abbia deciso di ottenere una certificazione IMQ.
La norma di riferimento è la norma CEI EN 60598-1 “Apparecchi di illuminazione. Parte1: Prescrizioni generali”.
Ma vediamo cosa succede in laboratorio. I tecnici controllano innanzitutto che l’etichetta e le stampigliature messe dal costruttore abbiano tutte le informazioni previste dalle norme a tutela del consumatore: nome o marchio del fabbricante, riferimento di tipo, tensione nominale, potenza nominale espressa in watt, classe di isolamento e altri dati, quelli ad esempio necessari per una corretta installazione. Tutti questi dati, che fanno parte della cosiddetta marcatura, devono essere riportati in modo chiaro ed indelebile.
In questa prima fase verificano pure la validità delle istruzioni per il corretto funzionamento dell’apparecchio.
Anche i componenti sono ispezionati uno ad uno e devono essere già stati certificati, cioè devono soddisfare i requisiti dalle norme ad essi relativi: cavi, portalampade, dispositivi di connessione, spine, interruttori, alimentatori ed altri.
Fino ad ora il trattamento riservato al nostro apparecchio, è stato tutto sommato abbastanza gentile, si è trattato di un esame a vista. Il gioco duro comincia adesso con la verifica della resistenza meccanica di tutte le viti. La prova viene eseguita con un cacciavite dinamometrico.
Dopo aver collocato nel morsetto un conduttore rigido di rame della massima sezione consentita, le viti vengono serrate ed allentate per cinque volte con un momento torcente di 0.5 Nm per le viti di 3 mm di diametro, se il diametro è superiore si aumenta il valore del momento torcente.
Con uno speciale martello di prova i tecnici verificano la resistenza meccanica di vetri, calotte e altre parti destinate alla protezione. L’energia d’urto sprigionata dal martello sulle parti fragili (vetro)di un apparecchio fisso è di 0.2 Nm mentre sulle altre parti è di 0.35 Nm.
I bambini per passione, e i grandi per errore, hanno la curiosa tendenza a toccare tutto, anche le parti più nascoste. Per questo vengono verificate le protezioni contro la scossa elettrica. Con un apposito dito di prova, collegato ad un circuito elettrico che segnala i contatti, il tecnico verifica che le parti in tensione non possono essere toccate, neanche volendo.
Per gli apparecchi in classe I, si prova la continuità del circuito di terra ovvero si verifica che le parti metalliche accessibili, quando l’apparecchio è installato o aperto per la sostituzione della lampada o per la pulizia, che possono andare in tensione per un guasto all’isolamento siano collegate in modo permanente e sicuro ad un morsetto o ad un contatto di terra e che tali connessioni abbiano una bassa resistenza. La conformità alle prescrizioni normative si verifica mediante un esame a vista e facendo passare tra il morsetto o il contatto di terra e ciascuna delle parti metalliche accessibili una corrente di almeno 10 A alimentata da una sorgente non superiore a 12 V. Si misura la caduta di tensione tra il morsetto o il contatto di terra e la parte metallica accessibile; la resistenza si calcola in base alla corrente e alla caduta di tensione. In nessun caso deve superare 0,5 ohm.
Le prove continuano. Si controlla la resistenza di isolamento con una tensione di 500 v in C.C.
I valori misurati non devono essere inferiori a quelli indicati dalle norme. Per fare un esempio, il valore della resistenza di isolamento misurato fra le parti che portano corrente e le parti metalliche di un apparecchio in classe II non deve essere inferiore a 2M ohm.
Si esegue poi la prova di rigidità dielettrica, prova questa che assieme alla precedente è molto importante per verificare la sicurezza elettrica e cioè avere garanzie contro le scosse elettriche. Fra le diverse parti si applicano valori di tensione diversi a secondo del tipo di apparecchio. Per un apparecchio in classe II, ad esempio, si applicano 1500 V in C.A. fra le parti in tensione di diversa polarità mentre si arriva sino a 3750 V fra le parti in tensione e le parti accessibili all’utilizzatore.
Gli apparecchi di illuminazione che possono essere usati anche all’esterno sono sottoposti ad una doccia infernale; è la prova per la verifica della protezione contro l’ingresso dei liquidi. 40 ugelli fissati su un arco rotante rovesciano con forza sull’apparecchio acceso molti litri d’acqua ininterrottamente per 20 minuti. Naturalmente la prova è superata se, al termine di un tale diluvio, nell’involucro dell’apparecchio non è penetrata acqua in modo da pregiudicare la sicurezza.
Prova analoga, ma con altro elemento: ecco la prova di protezione contro la polvere. Si chiude l’apparecchio in una camera ermetica e lo si sottopone per 180 minuti ad una tempesta di talco, una polvere molto fine. La prova è superata se la polvere non è entrata nell’involucro.
Una prova importante, che in qualche modo è la verifica delle altre prove, è quella di durata. L’apparecchio è messo in un ambiente a 35° per 168 ore che consistono in sette cicli successivi di 24 ore. Per ogni ciclo viene mantenuto acceso per 21 ore e spento per le restanti 3 ore. Al termine di questa estenuante esibizione il nostro apparecchio deve essere efficiente e sicuro come prima.
Ora vediamo la prova di riscaldamento. Si alimenta l’apparecchio con una tensione che produca 1,05 volte la potenza nominale della lampada di prova (nel caso di lampade ad incandescenza) e al raggiungimento della stabilizzazione termica dell’apparecchio (circa dopo 3-4 ore) si misurano le temperature nei diversi punti, temperature che non devono superare in nessun caso valori che potrebbero compromettere la sicurezza.
E infine le prove del calore e del fuoco. Le parti in materiale isolante che forniscono protezione contro la scossa elettrica vengono poste in un forno alla temperatura minima di 125°. Sulla superficie della parte in prova viene premuta, con una forza pari a 20N, una sfera d’acciaio del diametro di 5 mm. Dopo un’ora la sfera viene rimossa dalla parte che viene successivamente raffreddata per 10 s in acqua fredda. Se l’impronta lasciata dalla sfera non è superiore ai 2mm la parte ha dimostrato di essere resistente al calore e quindi la prova è superata.
Le parti in materiale isolante che tengono in posto le parti in tensione devono dimostrare invece di essere resistenti alla fiamma. Un campione di tali parti viene esposto per 10 s alla fiamma nel punto in cui con maggiore probabilità si sviluppano le temperature più elevate. La prova viene superata se, dopo che la fiamma sia stata allontanata, la combustione non dura più di 30 s.
Le prove che abbiamo descritto, che come abbiamo detto sono solo alcune delle 200 fra prove e verifiche stabilite dalle norme, richiedono una grande quantità di attenzione, di competenze e di sinergie, oltre che un tempo di almeno quindici giorni lavorativi. Ci danno l’idea di quale sia la garanzia fornita da una certificazione IMQ: la sicurezza di essere sicuri.